Basic overview:
A two-shot mold is a specialized mold formed by combining two or more sets of components, capable of producing two types of plastic materials.
The two-color molding machine is divided into horizontal and vertical types, with two or more sets of molds loaded and rotated by the machine for injection molding at 180 degrees or 120 degrees twice.
The two-shot injection molding machine is similar to the traditional single-color injection molding machine, but it differs in that it has two molding nozzles and a different molding action mechanism
I. Characteristics of Plastic Materials
Double-color and double-material refer to two types of plastic materials in two colors. Plastic materials are usually divided into hard plastic and hard plastic-encapsulated, soft plastic and hard plastic-encapsulated. (Hard plastic commonly used ABS PC PP PVC… Soft plastic commonly used TPU TPE TPR); the molded products have many functions such as appearance, texture, anti-collision and anti-falling.
Second, the way of encapsulation determines the basic structure of the two-color mold
Half-pack or insert uses 2 or more mold bases to rotate and perform 2-shot injection molding; full-pack uses a single integrated mold base that rotates with the moving plate and performs 2-shot injection molding
III. Product Structure
The method of encapsulation determines the basic structure of the two-color mold; for semi-encapsulation or insert, two or more mold bases are rotated and two injection molding processes are used; for full encapsulation, a single integral mold base is rotated by a moving plate and two injection molding processes are used. Mold base and assembly diagram
Fourth, mold structure
The two-color mold base is made of S60C high carbon steel; the mold base requires extremely high precision standards; the internal mechanism must be processed in four directions, and the same specification plates can be arbitrarily flanged, rotated, and interchanged to meet the overall accuracy requirements. The positioning ring usually uses a diameter of Φ120 or Φ150; the mold base must use the ‘Fudeba’ standard.
Note: The thickness of the two sets of mold bases must be the same; the outside of the upper and lower fixing plates of the mold base must be rotated to avoid C-angle; the fixed mold must be fastened with through screws to ensure safety, and must be removed during the stripping process
Plate mother die: make corresponding concessions on the die foot to facilitate the disassembly and assembly of screws
V. Processing flow
Do a good job of structural review before mold opening to understand the mold processing technology.
The master mold needs to retain the corresponding pre-pressing (0.05-0.10mm) for the second time.
The conventional two-color male mold is identical and can be processed simultaneously.
The precision of the mold base must be tested, and any mold base that does not meet the tolerance requirements must not be used.
VI. Two-color mold clamping program
The master mold and two sets of male molds are simultaneously clamped together (the master mold is painted with red lead and the male molds are trimmed), until the two sets of male molds are aligned and perfectly fit together.
→ Take any set of male molds and combine them with the secondary female molds until they are completely matched (painting the male molds with paint and repairing the secondary female molds).
Do a good job of detecting the actions before testing the mold, and do not miss or install the mold incorrectly on the machine (incorrectly installing the mold will result in scrapping more than 2 sets of mold cores).
Two-color module vertical plane example (A typical two-color)
Two-color module vertical plane example (B middle plate two-color)
Precautions for mold forming:
1: Formwork erection:
a: Remove all clamping screws before setting up the mold
b: First, set up a full mold and reverse the operation side without adjusting the mold to high pressure, otherwise the moving mold will be damaged due to uneven stress on the machine;
c: Only after all the clamping screws are installed by hand can they be locked tightly
d: After the mold is opened, the male mold rotates 180 degrees;
e: Load the secondary master mold based on the primary master mold;
f: Finally, install the secondary male mold based on the secondary female mold;
g: After the two sets of mold racks are set up, adjust the mold
2: Molding production:
a: Determine whether the two raw materials are correct;
b: Set the ejection; generally, the first ejection side is closed and the second ejection side is open;
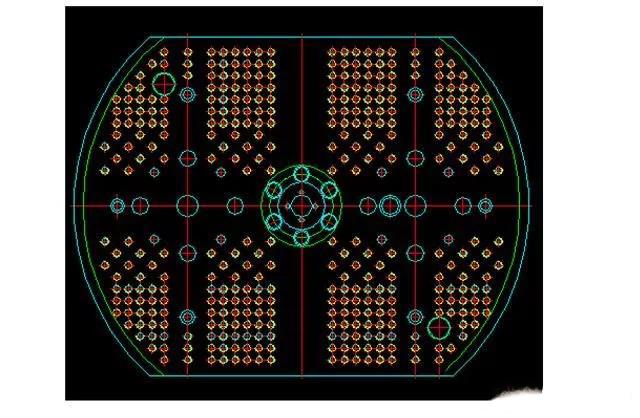
Product examples
Product example: Electroplating after the formation of two-color products
Product examples
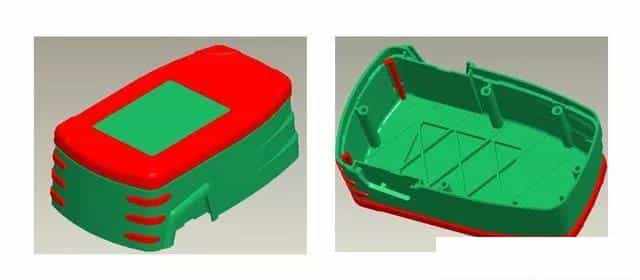
Considerations in design:
1: Before using the two-color mold, it is important to understand the parameters of the molding machine
(dimensions and location of screw holes, dimensions and location of ejection rods, dimensions and location of rotating shafts);
2: The operation side of the two-color machine is the same as that of the monochrome machine. If the mold is a three-plate mold with small water inlet for one injection, a material flow device is required for the one-time material flow channel to facilitate fully automated production
(The operator is located on the secondary side, and the primary material head cannot be accessed);
3: The soft rubber product and the material bone should have skin texture (soft rubber characteristics: strong adhesion to smooth walls).
The first injection must be able to automatically cut the gate to avoid residual protrusions that can cause secondary coating and form defective products;
The secondary injection should be carried out in concealed areas of the finished product (latent, horn, bottom overlap);
4: The insert class needs to first run through the mold with a finished product, which can be done using a public mold ‘seesaw’
The mechanism or the parent mold is inserted with a needle, and the insert is inserted through the hole.
5: When two types of glue are mixed, the temperature of the secondary glue should be lower than that of the primary glue (if the temperature of the secondary glue is higher than that of the primary glue, it will burn the primary glue and produce defective products); mixing hard glue with soft glue is not feasible.
(Due to the consideration of finished product power consumption, the dual-color mobile phone buttons are taken from PC once and ABS twice.).
6: The shrinkage of the double-color secondary plastic material must be the same as the first time, and the depth and side wall pressure sealing type position need to leave a pre-pressing allowance of 0.05~0.10mm (controlled by CNC, design needs to be specified)
Two-color molding technology: preliminary design and manufacturing principle overview
Precautions for assembling and testing the mold
1: The fluidity of soft rubber is particularly strong, and it must be controlled well during secondary molding
The sealing degree of each part and the exhaust slot are controlled within 0.015mm (its fluidity is similar to nylon)
2: For the secondary and primary rubber level mating surfaces, in addition to considering the secondary pre-pressing value, it is also necessary to ensure proper secondary exhaust, with the exhaust slot controlled at 0.03-0.06mm
(Due to the elasticity of primary plastic materials, secondary molding, especially soft plastic, is extremely prone to air pockets and hot secondary melt defects that are difficult to control during primary molding.) The effectiveness of repairing secondary formed burrs and air pockets caused by primary compression depends largely on the engineering site’s handling strategies during the molding process (corresponding to adding or subtracting glue, reinforcing, blocking glue, and exhausting air).
3: The smooth operation of the pouring system and ejection system is also a prerequisite for ensuring the smooth production of molds. A good two-color mold must have a reasonable structure, accurate design, and exquisite manufacturing process in the early stages to achieve success.
Preliminary design of two-color molding technology ~ overview of manufacturing principles
Conclusion:
From the characteristics and applications of multi-color injection molding and dual-material injection molding, it can be seen that there is a trend to replace the molding process in the future. Innovative injection molding technology not only improves the precision of the injection molding process, provides high-difficulty process technology, but also expands the scope of the injection molding process. Only with innovative injection equipment and processes can we meet the increasingly diverse, high-quality, high-value-added product demands. The application of innovative injection molding technology is imperative. Preliminary design of dual-color molding technology ~ overview of manufacturing principles.